Continuous Process Distiller
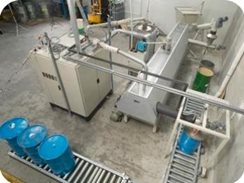
The Continuous Process Distiller was designed for high capacity requirements. It is capable of treating 5 times the amount of fluorescent powder and other low organic materials compared to a standard Batch Distiller. This ability to process large volumes of material results from the distiller's non-stop operation: it may be run 24 hours a day.
The Continuous Process Distiller incorporates the technology from the traditional Batch Distillers, however, the traditional dome is replaced by a drum made of heat and corrosion-resistant steel. Mercury-contaminated materials are continuously transported through this steel drum and are heated to temperatures of 500 - 700ºC.
During the heating process the mercury vapours are released from the waste material and continuously transferred to the cooling system where the mercury condenses into free floating liquid mercury. The reclaimed mercury has an average purity level of 99,99%, depending on the mercury concentration before processing.
TECHNICAL DATA:
|
|
Performance: |
|
Capacity |
: Approx. 600l powder or
exhaust tubes/24h |
Hg Emission to Atmosphere |
: Max 0,025 mg/m3 |
Hg Concentration in Waste |
: Max 0,05 mg/l |
Hg Purity |
: Up to 99,99% |
Degree of Recovery |
: Up to 99,99% (depending on
processed material) |
|
|
Dimensions: |
|
Approx. space required for installation |
: 50 m2 |
|
|
Consumption |
: Approx. 25 kW |
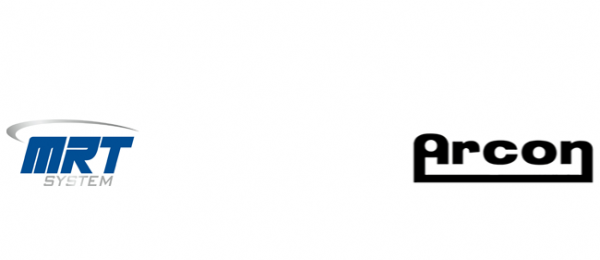