Lay Out - WEEE Line
The Eldan Shredder S1000 WEEE Recycling Plant comprises the following equipment.
The plant has an input capacity of approximately 3-4 tonnes per production hour, depending on the input material.
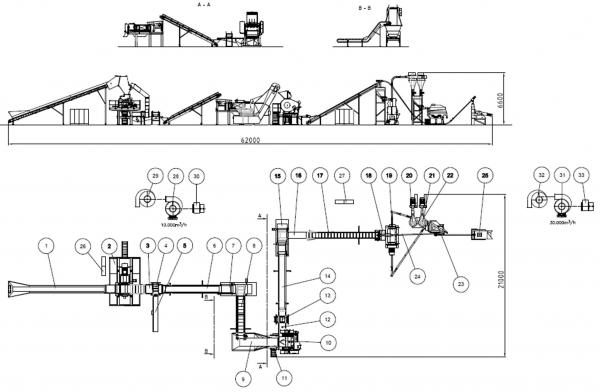
Pos. 1 One Inlet Conveyor. Drive pulley Ø215 mm. W x L is 800 x 14400 mm.
Installed Power 4 kW.
Pos. 2 One Shredder S1000 with rotor length of 1000 mm and motor power of 250 kW.
The machine is equipped with 28 impact rings and 4 impact beams. The lower part of the housing supports the rotor as well as the two grate retainers which contain 2 and 3 grate segments. Both grate retainers are opened and closed hydraulically. The motor for opening of upper part, hopper, grate retainer and oversize reject door: 3,0 kW. The Shredder includes a Service Platform.
Pos. 3 One Vibratory Discharge Conveyor. W x L is 1000 x 5000 mm.
Installed Power 3,15 kW.
Pos. 4 One Electromagnet (Electromagnetic Belt Separator) type 451-60/140-290-S0 to separate iron particles from the material flow. The Electromagnet is arranged beyond a Conveyor Belt and separates iron particles automatically. The material does not get in contact with the magnetic system itself and can thus be damp, sticky and have a temperature of up to 150ºC.
Weight: 1475 kg
Overall dimensions: 2545 x 1200 mm (L x W)
Magnetic Unit: 600 x 1400 x 290 mm (W x L x H)
Effect of magnet: 2,6 kW
Effect of drive motor: 1,5 kW
Pos. 5 One Outlet Conveyor. Drive pulley Ø160 mm. W x L is 600 x 5000 mm.
Installed Power 1,0 kW.
Pos. 6 One Inlet Conveyor including drum magnet with Ø215 mm. W x L is 800 x 7900 mm. Installed Power 2,2 kW.
Pos. 7 One Eddy Current System (Non-ferrous Separator) 0428-25/90 consisting of the following:
One Vibrating Feeder for detaching, smoothing and feeding the material to the
Non-ferrous Separator.
Drive motor: 2 x 0,8 kW
One Non-ferrous Separator for separating the metal particles in the mixed fraction.
Feed speed: approx. 0,3 m/sec.
Belt speed: 0,5 – 2 m/sec. variable
Drive motor for magnet rotor: 4,0 kW
Drive motor for belt conveyor: 1,5 kW
One Stand and Service Platform
Pos. 8 One Conveyor. Drive pulley Ø165 mm. W x L is 800 x 7500 mm.
Installed Power 2,2 kW.
Pos. 9 One Tumble Back Feeder to feed at an even, controllable rate to the Multi Purpose Rasper. It consists of Heavy Duty sidewall steel skirts and structural steel support, an approx. 5 m3 loading hopper and a 1,220 mm wide fabricated rubber and steel conveyor belt, which is driven by a 3,7/4,4 kW electric motor through a Heavy Duty jackshaft mounted gear box.
Frequency variable speed control for precise flow metering.
Main dimensions L x W x H: approx. 6,1 x 2,3 x 5,4 m
Speed variation @ 50 Hz 2,9 – 5,7 m/min
Pos. 10 One Multi Purpose Rasper type MPR120 with rotor length 1200 mm and 144 rpm rotor speed. The rotor is driven by a V-belt transmission and powered by 1 pcs. Installed Power 132 kW electrical motor. The machine is supplied with 15 flying and 16 static knives and screen. The main housing is equipped with replaceable wear plates, wear rings and other components. Hydraulic, motorised opening of infeed hopper/upper housing and screen cradle.
Pos. 11 One Service Platform to be used during service and maintenance work on the
Multi Purpose Rasper.
Pos. 12 One Vibratory Discharge Conveyor. W x L is 800 x 5000 mm.
Installed Power 1,5 kW.
Pos. 13 One Overband Magnet DM1450 for steel removal. Installed Power 0,55 kW.
Pos. 14 One Inlet Conveyor with drum magnet Ø215 mm. W x L is 1000 x 7200 mm.
Installed Power 2,2 kW.
Pos. 15 One Eddy Current System (Non-ferrous Separator) 0428-25/90 similar to Pos. 7.
Pos. 16 One Conveyor. Drive pulley Ø165. W x L is 800 x 4000 mm.
Installed Power 0,75 kW.
Pos. 17 One Inlet Conveyor. Drive pulley Ø165. W x L is 800 x 12000 mm.
Installed Power 2,2 kW.
Pos. 18 One Silo type SMV with approx. 1 m3 volume. The purpose of this Silo is to balance the output from the Granulator to the maximum input rate of the Separation Table, thus ensuring that the quality of separation is maintained. Installed Power 0,8 kW.
Pos. 19 One Heavy Granulator type HG169 with rotor length 1600 mm, rotor speed 400 rpm and motor power 110 kW. Supplied with 20 flying and 8 static knives and screen. The main housing is equipped with replaceable wear plates, wear rings and other components. Hydraulic, motorised opening of infeed hopper/upper housing and screen cradle.
Pos. 20 One Pneumatic Material Transport. Installed Power 23,5 kW.
Pos. 21 One Pneumatic Material Transport. Installed Power 23,5 kW.
Pos. 22 One Silo type SMV, with approx. 1 m3 volume. The purpose of this Silo is to balance the output from the Granulator to the maximum input rate of the Separation Table, thus ensuring that high quality of separation is maintained. Installed Power 0,4 kW.
Pos. 23 One Separation Table C22. The Separation Table is designed to separate the metal from the insulation. The output from the Separation Table is divided into 4 output fractions: dust, metal, plastic, middling. The deck surface is 1,44 m2, power for deck and fan motor 1,1 + 11,0 kW.
Pos. 24 One Flexible Screw Conveyor, middling return. Installed Power 1,1 kW.
Pos. 25 One Classifier type PC12. The Classifier will effectively remove copper and aluminium fines from the plastic fraction. It consists of two layers of screens and a bottom tray. Motor power: 0,75 kW.
Pos. 26 One Electrical Power Unit for Pos. 1-7, 28.
Pos. 27 One Electrical Power and Control Board for Pos. 8-25,29
Pos. 28-30 Jet Air Filter JM 21/45-06 4TR T3 for 10,000 m3/h air flow, for efficient high pressure, low volume shock blast cleaning. The filter is of circular design, comprising:
-
Top section with compressed air tank approved (according to EN286-1 norms) and
solenoid membrane valves giving an adjustable, automatic short air shock blast to one
filter section at a time, monitored by an electronic control system
-
Electrical PC control with adjustable time and pulse function and connections for
remote reading
-
Textile filter bags with total filter area 41 m2 and suspended filter cages
-
Bottom section with conical discharge and air lock 1,5 kW
-
Support legs
-
Ventilator 18,5 kW
Pos. 31-33 One Jet Air Filter JM 70/40-06 4TR T3 for 30,000 m3/h air flow, for efficient high pressure, low volume shock blast cleaning. The filter is of circular design, comprising:
-
Top section with compressed air tank approved (according to EN286-1 norms) and
solenoid membrane valves giving an adjustable, automatic short air shock blast to one
filter section at a time, monitored by an electronic control system
-
Electrical PC control with adjustable time and pulse function and connections for
remote reading
-
Textile filter bags with total filter area 123 m2 and suspended filter cages
-
Bottom section with conical discharge and air lock 1,5 kW
-
Support legs
-
Ventilator 45 kW
Please note:
The filter is to be connected to a screw or piston compressor (approx. 7,5 kW) for
500 Nl/min air consumption at 2-4 bar – not included.
The Filter System includes one Front Cyclone with air lock (1,5 kW).
The Filter System includes aspiration ducting including bends, valves,
size reducers, supports.
The emission from this type of Filter System is max. 10 mg/m3 dust.
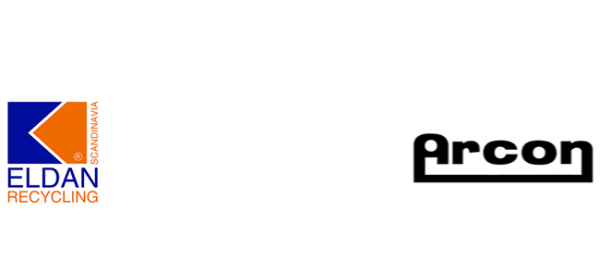